Veneer Faces
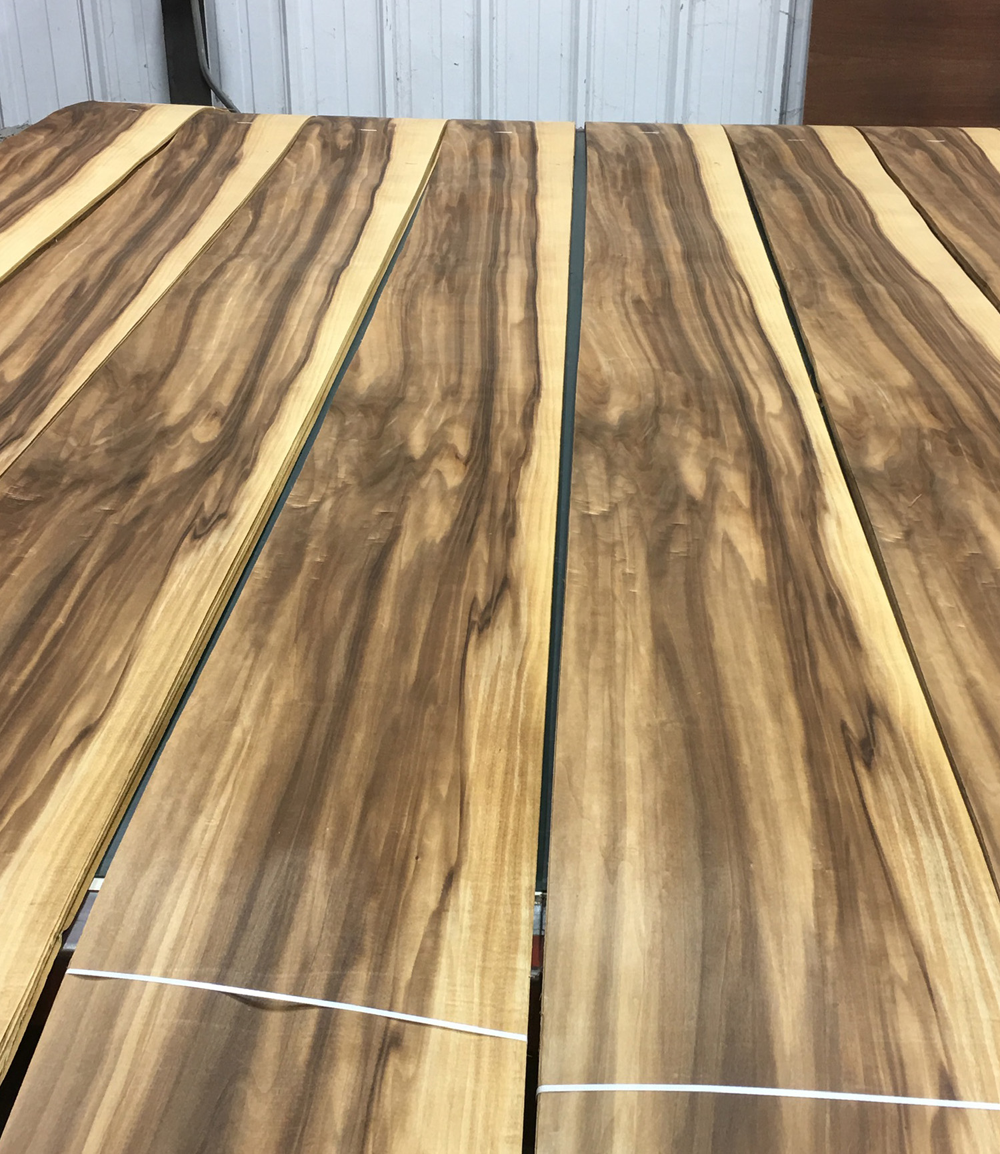
With the shop drawings and panel list in hand, we mark the veneer with chalk so the clipper will know how we want the bundles clipped to make the component width for each leaf of veneer within the face(s), which will eventually be pressed onto the selected substrate.
All requirements for matching the adjacent veneer leaves within the face, panel and elevation are typically discussed with the design team at the time of specification, prior to when bidding takes place or production of any kind.
Allowable inclusions from nature are also discussed, so that there are no questions regarding the visual expectations and how the veneer is to be used.
Production of the raw faces is a critical control point to maintain your design intent.
Test runs are often made, during which we provide samples or photos of the veneer face, based upon the intent discussed with the architect for their final approval prior to continuing the process.
Examples of raw faces that have been spliced together. The edges of the veneer are glued and seamed under pressure. Veneer tape is used to reinforce the seams, and will be sanded off later once the face is pressed onto the final substrate.
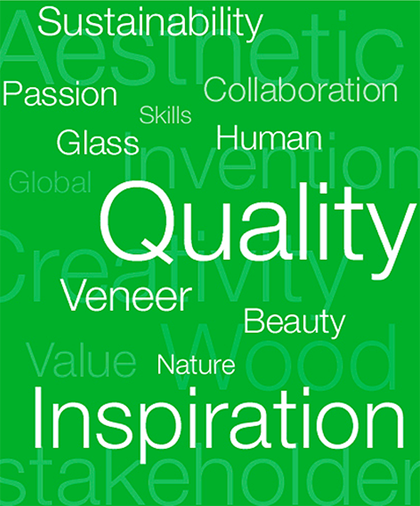
Continue to Sheet Goods | Continue to Panel Products | Go back to Custom Wood Solutions
We appreciate your visit and hope to hear from you soon!
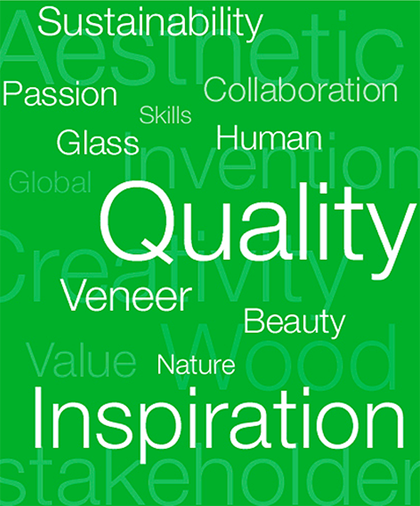
Corporate Offices
6 Woodfield Road
Green Township, NJ 07821 USA
- Phone: 973-786-4079
- Fax: 973-786-4077
- Email: info@scottbrogangroup.com
- Join Our List
Scott G. Brogan, CEO
Jon A. Kelsch, Operations
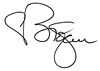